My 6 Best Tips for Rigid Heddle Warping Success!
I absolutely love direct warping my rigid heddle looms! It’s one of the fastest and easiest ways to get started on a new weaving project, and I find the process simple and satisfying. There’s nothing better than going from an idea to a fully warped loom in hardly any time at all.
But let’s be honest—direct warping isn’t foolproof. If you’ve ever ended up with a tangled mess, uneven tension, or felt completely frustrated before you even started weaving, you’re not alone! I’ve made plenty of mistakes over the years, but the good news is that most warping issues have quick and easy fixes. In this post, I’ll walk you through some of the most common direct warping mistakes and how to solve them so you can begin to enjoy the warping process as much as the weaving!
So, What is So Great About Direct Warping?
When you begin to make the warp for a table loom or floor loom, you traditionally do so with a warping board, or with a sectional beam setup. These methods are terrific as they allow the weaver to be precise about the warp making process, but I’m not kidding when I say they take time!
Direct warping a rigid heddle loom though, allows us to side step other processes, to start and finish our warp at the loom and sometime to even skip the threading afterwards by doing it during the warping!
We use a direct warping peg, clamped at a suitable distance away from the loom (the distance will depend on your warp calculations so be sure to do that first). We tie the yarn onto the back apron rod of the RH loom, take a loop through the heddle/reed and then drop the loop onto the peg. Back to the loom and repeat.
This makes the process really fast and hey, you even get some exercise thrown into the deal as you go from the loom to the peg and back again! 💃
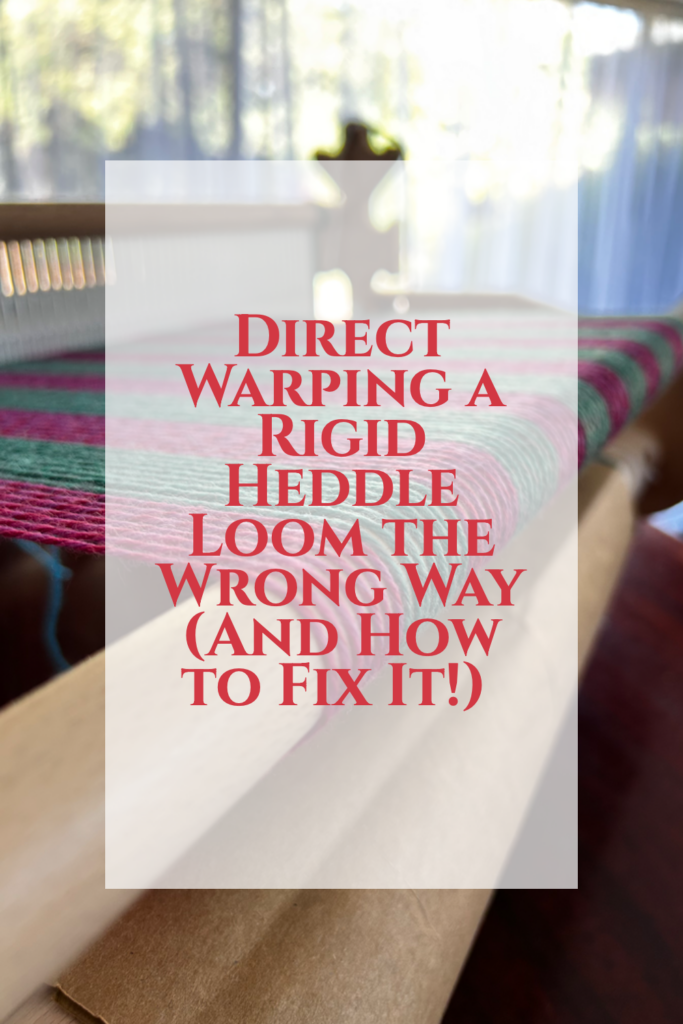
6 Common Warping Mistakes & How to Fix Them
- Forgetting to Take the Warp Over the Front & Back Beams
This is a very common rookie weaver error, so don’t worry if you have fallen victim to it, we’ve all been there!
- Why it’s a problem: Most of the time you will be unable to make a shed. You put your heddle up, you put it down, nothing happens!
- How to fix: This depends on your particular rigid heddle loom. Some have beams that are removable while you have a warp on – if this is the case with your loom, remove whichever beam you have warped under, slacken your warp tension and place the beam back so that it is underneath the warp.
- If you can’t remove your beam/s you will need to un-warp and re-warp correctly over both beams.
2. Using the Wrong Yarn (Stretchy Acrylic, etc.)
This can be a bit of a weaving nightmare because you don’t always know just how the yarn will perform under tension if you haven’t used it before. Once stretched, you can’t “unstretch” the yarn.
- Why it’s a problem: Stretchy yarns make it hard to maintain even tension. They will frequently stretch more and more as you advance your warp and try to weave, no matter what you do.
- How to fix: You can try using wedging and tension improving techniques. I once wove with an acrylic yarn that began to stretch and by using these techniques I was able to finish the project, but I can tell you, it wasn’t fun! The only other alternative is to (and I don’t say this lightly, it’s not my usual recommendation!) bin the warp and start over with a different yarn. I hate having to tell someone to do that, but it’s a good lesson in what is an inappropriate yarn for warping.
3. Too Many Warp Ends on One Peg
Bunching up too much warp on one peg when direct warping is less than ideal for a couple of reasons.
- Why it’s a problem:
- Your warp should be well ordered on the peg, each warp loop being placed above the last one to keep the threads in good order.
- If you don’t distribute the warp among more than one peg (especially if its a wider warp) you will have more wasted yarn as it has to travel further to go to a central point (the peg).
- Your warping peg can lose tension. Too much warp on a single peg can cause too much pressure, causing the peg to go pinging across the table and messing up the lovely order of your warp!
- How to fix: Distribute warp ends across more than one peg. Don’t place too much tension on the warp as you take the loops around the peg. Aim for consistency, not tightness.
4. The Wrong Attitude: Warping Frustration
I don’t know about you, but when I’m frustrated I don’t think clearly! Usually, the way you think about your warping before commencing is how it will be. For example, I think of warping as simple and easy, so when I go through the warping process, guess what? It’s simple and easy!
- Why it’s a problem: Leads to mistakes and makes the process feel stressful. Clouds judgment and clarity of thought.
- How to fix: Take breaks, set up in a calm environment, and remember that practice makes perfect! Give yourself plenty of grace, you’re not expected to know everything, it’s a journey! If you have a recurrent frustration, perhaps it’s time to do some more research or take a step by step class to help you get over the hurdle.
5. Warping the loom or heddle backwards
- Why it’s a problem: You won’t be able to advance your warp forwards if it’s warped on the front beam instead of the back. Warping the heddle backwards is not as big of a deal – you can actually weave that way but it may be less comfortable to use. If you have warped your heddle backwards and want to repair it, this video will show you how.
- How to fix: You can fix a backwards warped loom by cutting your yarn loops at the peg and securing with a choke tie. Wind this warp onto your front apron rod (if you haven’t done so already). Leave enough length at the other end to tie on the cut ends to the back apron rod securely. You can then release the tension at the front apron rod and begin to roll onto the back beam, using warp separation as you go. Once you have the warp rolled on to where it’s supposed to be, you can progress as normal!
6. Trying to hurry the process
- Why it’s a problem: Trying to speed through the warping process when you’re not all that familiar with it could be a recipe for disaster. You may skip steps, you may make mistakes, you may get tangles, things may go wrong and you don’t notice. Rolling on a warp with good, consistent tension is not a step to be hurried over, it takes a little time and patience.
- How to fix: Warp your rigid heddle loom when you actually have time to do so. If you can’t get it done in one session (and it’s absolutely fine not to!) ensure that you have set up in a location where you can leave the warp partly done to come back to. If you’re warping at the dining room table at 5pm and your family needs to sit down to eat at 7pm, you may have a problem.
Final Tips for Direct Warping Success
- Slow down and check your work as you go. Time is never wasted in weaving, it is only invested 😉
- Use a checklist to tick off as you go (I have a free printable one here) to ensure you don’t miss any steps in setting up your loom.
- If you make a mistake, don’t panic—ALL issues can be fixed!
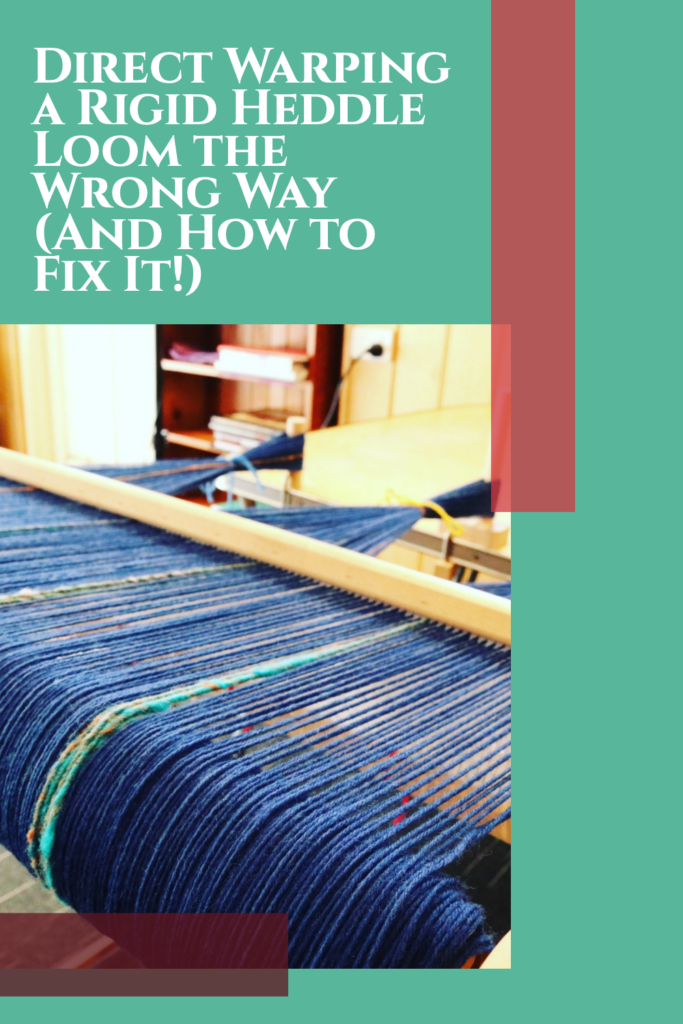
Want to learn more about warping successfully? Check out this list:
5 Tips for Rigid Heddle Warping
Setting Up for Success Online Workshop
Did you know that I’m a reseller for Lojan Wheels and Looms in Australia? If you are interested in knowing more, please feel free to contact me.
Until next time…
Happy Weaving!
*This post contains affiliate links. For further information, please see my disclosure policy.