If you’re a weaver, knitter, crocheter or fiber artist, chances are you have a stash of leftover yarn—those little bits and ends that seem too small for a full project but too precious to toss. Instead of letting them pile up, why not turn them into beautiful, functional woven projects?
Yarns can be expensive and it’s just great practice to aim to minimise yarn waste from your weaving projects.
In this post, I’ll share 10 creative ways to use leftover yarn in weaving—from small home décor items to quick and easy gifts. Whether you’re passionate about reducing fiber waste or just love experimenting with colors and textures, these ideas will help you make the most of every last strand!
1. Woven Coasters (Perfect for Small Scraps!)
Why It’s Great:
Woven mug rugs and coasters are ideal for using up short lengths of yarn. They’re small, quick to make, and perfect for gift-giving.
How to Make It:
- Use a small loom or a cardboard loom or potholder loom.
- Mix different textures and colors for a fun, scrappy effect.
- Finish the edges with tassels or a simple hemstitch.
👉 Bonus Tip: Group coasters into sets of four and tie them with twine for a charming handmade gift!

2. Wall Hangings and Tapestry (Mix Colors & Textures!)
Why It’s Great:
Wall hangings allow you to mix and match yarn types while embracing an eclectic, bohemian style.
How to Make It:
- Use a branch, quilt hanger or dowel rod as the top hanger.
- Weave different textures (chunky wool, cotton, embroidery thread) for depth.
- Add fringe, loops, and knots for a playful, freeform look.
👉 Bonus Tips: Try an ombre effect by weaving from dark to light shades of the same color.
: Krokbragd is a wonderful weave structure for wall hangings. Check out the Krokbragd 101 Online Course to learn how to weave many krokbragd designs and a a striking wall hanging on your rigid heddle loom.
3. Bookmarks (Quick & Easy Gifts!)
Why It’s Great:
Perfect for thin yarn scraps, bookmarks make charming and practical gifts for book lovers.
How to Make It:
- Warp a narrow warp on a small loom.
- Use finer yarns for a lightweight feel and reduce bulk.
- Finish with braided or beaded tassels or a short, hemstitched fringe.
👉 Bonus Tip: Personalize it with initial embroidery for a thoughtful touch!
4. Woven Bracelets, Keychains and Key Fobs
Why It’s Great:
Turn colorful yarn leftovers into fun, wearable accessories!
How to Make It:
- Use a small loom or inkle loom for sturdy, structured pieces.
- Experiment with geometric patterns for a modern look.
- Attach a keyring or metal clasp for finishing. Use key fob hardware for a professional and simple finish.
👉 Bonus Tip: Sell these at craft fairs or bundle them with other handmade items!
5. Wrist Warmers
Why It’s Great:
Keep your hands and wrists warm without constricting your fingers!
How to Make It:
- Weave individual small panels to stitch together or use a tubular method.
- Hem any raw edges for sturdiness.
👉 Bonus Tip: Choose coordinating colors for a more cohesive design! You could even choose colors to match your favourite outfit.
: Check out the Wrist Warmers Online Class which uses a rigid heddle loom and tubular weaving to make a warm and groovy pair of wrist warmers!
6. Hat
Why It’s Great:
Hats are such a great item to make for yourself or to gift. You can customise the style to suit your own preferences. This one is also great for multi craftual people as you can incorporate techniques.
How to Make It:
- Weave either a piece to seam or a tube (a tube only requires one seam)
- Wool is great for snug and warm hats
- Either weave extra fabric for a turned up brim or knit/crochet a hat band that is stretchy.
👉 Bonus Tip: Make a pom pom to add on top!
: Judith Shangold has an excellent book – Weave, Knit, Wear that provides a lot of inspiration for woven garments, including hats.
7. Weaving for Mending & Embellishment
Why It’s Great:
Use weaving to patch clothing, bags, or even furniture!
How to Do It:
- Create woven patches to mend holes in jeans or jackets.
- Add decorative woven accents to hats, shoes, or pillows or on the back of a denim jacket as a panel.
👉 Bonus Tip: Try visible mending techniques for an artistic, eco-friendly touch!
8. Notebook Cover
Why It’s Great:
A notebook cover makes such a thoughtful gift as it’s both useable and beautiful.
How to Make It:
- All you need is a rectangle of woven fabric, appropriate to the size of the notebook you wish to cover.
- You can choose to line the cover with additional fabric or not.
- A cover can be as individualised as you like, let your imagination go wild!
👉 Bonus Tip: Use contrasting colors for a striped effect!
: This free Notebook Covers Project is the perfect place to get your started.
9. Woven Greeting Cards
Why It’s Great:
Handwoven details on cards or gift tags add a personal touch to gifts.
How to Make It:
- Weave a tiny strip and glue it onto cardstock. Or use some woven fabric scraps you already have.
- Cut a window from your card and stick your fabric in to look like a framed artwork.
- You could cut your fabric into shapes to stick on to the card.
👉 Bonus Tip: Pair with handmade envelopes for a complete set and a special gift!
10. Woven Ornaments
Why It’s Great:
Ornaments make wonderful seasonal decorations and can be made from the smallest yarn scraps.
How to Make It:
- Weave mini stars, hearts, or trees.
- Attach an inkle loop for hanging.
- Add gold thread or beads for extra charm.
👉 Bonus Tip: Make sets of handwoven ornaments for holiday markets or gifts!
: You can get started with this free tutorial for making Handwoven Christmas Ornaments.
*This post contains affiliate links. For more information, please see my disclosure policy.
Give Your Leftover Yarn a New Life!
By weaving with leftover yarn, you’re not only reducing waste but also creating something unique and meaningful. You made an investment when you purchased the yarn, so why not get the most out of it? Whether you turn your scraps into home décor, accessories, or gifts, these projects prove that no yarn is too small to be useful!
Pin & Save This for Later! 📌
Love these ideas? Pin this post on Pinterest so you can come back to it anytime!
Until next time…
Happy Weaving!
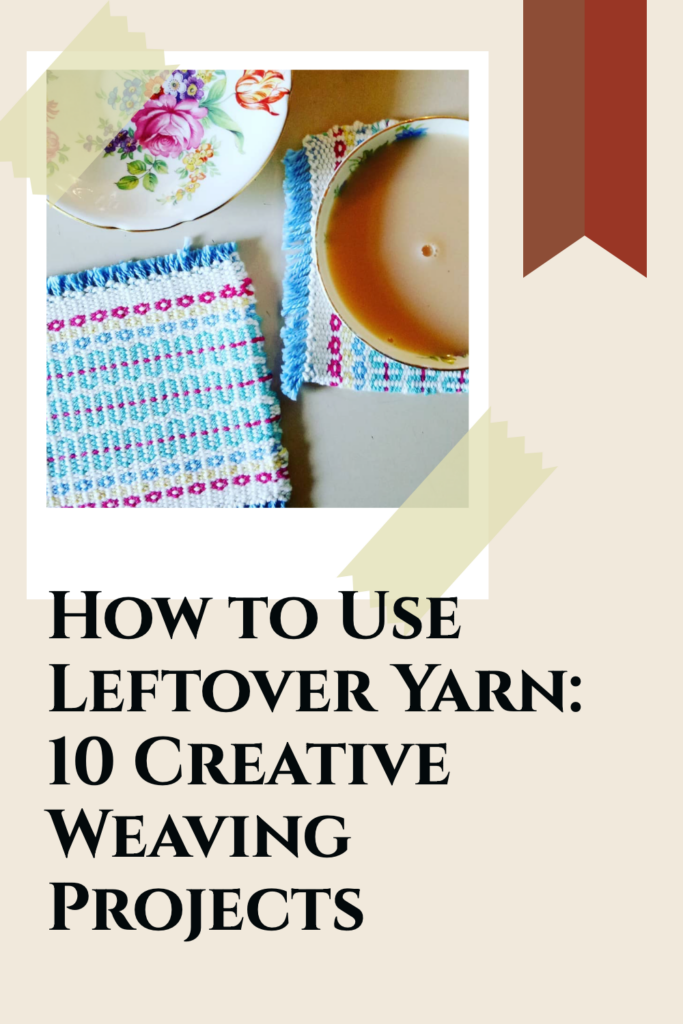