Weaving on a rigid heddle loom is an incredibly rewarding craft, but it’s not without its challenges.
Like learning anything new, time and patience are necessary to achieve your goals.
Something I have observed in my years as a weaving teacher is that most new weavers will experience the same issues that require troubleshooting. This is actually a good thing!
From a teaching perspective, I can identify problems that weavers are having very quickly by just looking at their work. And from a learning perspective, many weavers have gone before you with the same mistakes cropping up and there are many resources available to learn from to figure out where you went wrong.
Weaving should be relaxing, but common issues can unravel your peace.
Whether it’s uneven edges or frustrating warp tension issues, these common hurdles can leave weavers scratching their heads and feeling a bit disillusioned with the whole thing! The good news is that many of these problems are preventable with a little extra care, preparation and experience.
In this guide, we’ll explore why starting with a well-tensioned warp is essential, how patience in the setup process can save you from headaches later, and why taking the time to learn and reflect will make you a more confident and skilled weaver. Let’s turn those troubleshooting moments into learning opportunities!
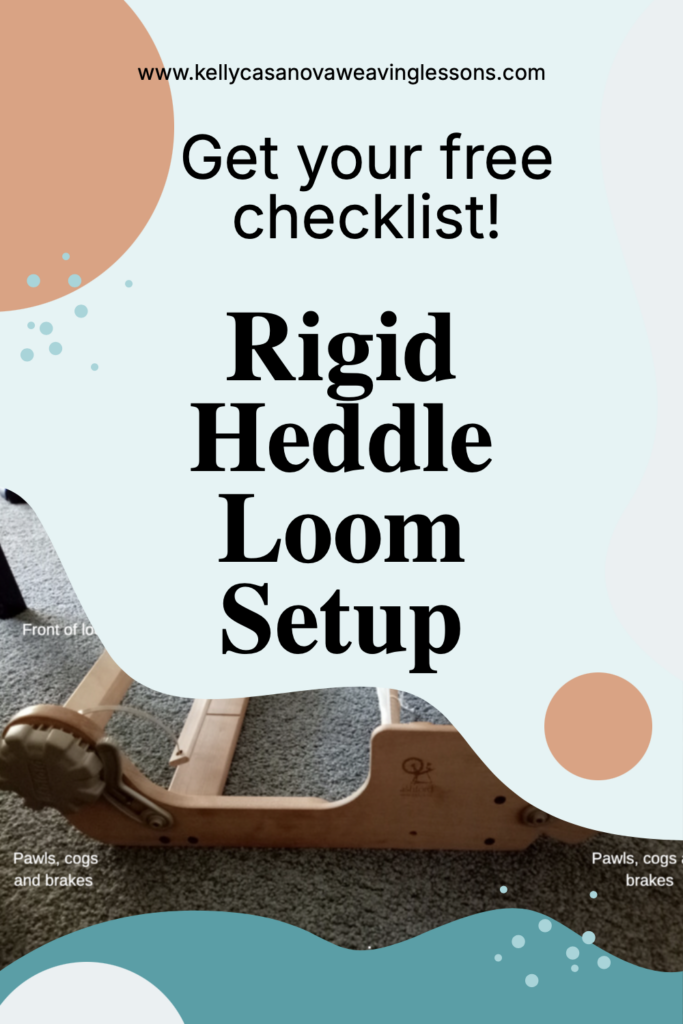
1. Why a Well-Tensioned Warp is Non-Negotiable
I have no data to qualify this statement, but I feel confident is saying that at least 90% of negative issues encountered in the weaving process are due to something being off with the warp.
Consistency is more important than firmness of tension.
By this I mean that in the warping process you should aim to have all of your warp threads under approximately the same amount of tension, or as near as you can get it.
It’s no good achieving great tension on your edge threads and poor tension in the middle. Or vice versa. The idea being that if your tension is consistent while warping you can then focus on the tightness of the tension afterwards and all the warp threads will be under the same amount of tension.
Uneven tension causes a huge range of headaches to the weaver. Skipped threads, inconsistent edges, uneven or wavy weft picks, snagged or diving shuttles, heddle positions not holding correctly… I could go on!
- How to achieve great warp tension:
There are so many methods for warping your rigid heddle loom and it’s definitely not a “one size fits all” process. In my last article I discussed the importance of great warp tension in more detail, so be sure to check that out.
I also recommend that you check out this playlist on Youtube for a variety of methods to consider:
- Quick tips for achieving good tension:
- Adjust tension gradually and evenly.
- Test warp tension by bouncing your hand across the warp once it’s tied on.
- Separate your warp prior to weaving
- Take your time and explore different methods to find one that works well for you.
2. The Virtue of Patience in Setting Up Your Loom – Don’t Rush!
There are many things in life that can be rushed and completed quickly. Weaving is not one of them 😆 Rushing will inevitably cause mistakes due to overlooking an important step or process, trust me on this one!
There is so much more to weaving than simply throwing a shuttle back and forth.
There is the planning of the project, sampling if necessary to ensure appropriate yarns and setts. There is the careful warping, threading and readying of the loom prior to weaving. There is the double checking to ensure correctness of threading and steps (especially important for newer weavers!) And that is all before we actually get to the weaving!
Embrace the process:
- If you feel impatient initially, try to let the process envelop you and teach you to go slowly.
- Setting up the loom is an integral part of the craft, enjoy it!
- Take breaks if you feel frustrated—it helps avoid costly errors and gives you a breather.
- Try to do your warping in a space where you can leave the loom if needed.
- Tips for setup success:
- Create a checklist for each setup stage so you don’t miss any steps.
- It can be great to have a helper for your first project at least. They can hold the warp for you so you don’t have to focus on more than one thing at once. Another set of eyes can also help to pick up errors you may overlook.
3. Giving Yourself Time to Learn and Reflect
This ties in very closely with the last point on patience, but is less about the physical weaving and more about your learning journey.
We all learn in different ways and to be effective we need to give ourselves a lot of grace when learning something new. Perhaps you are the type of learner who just “get’s it” right away or perhaps you are more like me and need more time.
One thing that I do frequently, and have since I started weaving, is to grab one of my weaving books off the shelf and quietly flick through to see what strikes me that day.
Repetition is so good and necessary for learning. There have been many concepts that I had convinced myself I was not smart enough to learn, but it just takes persistence and not giving up on yourself.
Weaving is a journey, not a race:
- Learning takes practice; each project builds skills. Start small and grow as you go.
- Mistakes are opportunities to learn and grow.
Tips for cultivating a learning mindset:
- Keep a weaving journal to note challenges and solutions.
- Reflect on what worked and what didn’t after each project, and why.
- Seek out advice and resources from weaving communities.
- Have good quality books in your weaving library to refer to over and over.
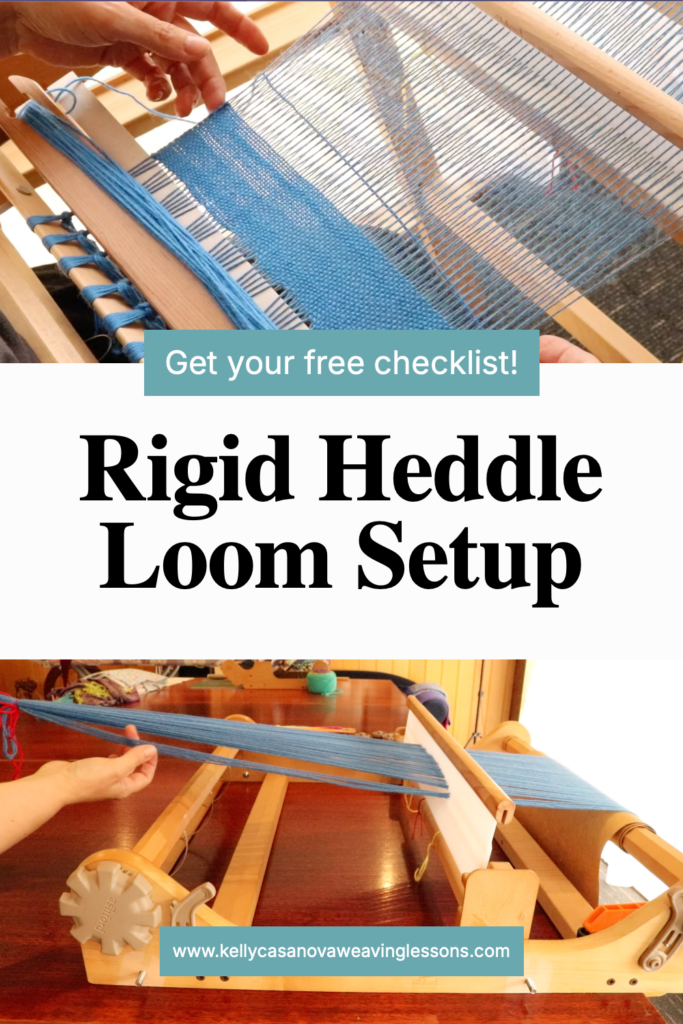
4. Troubleshooting Common Issues (and How to Avoid Them)
These are what I see to be the most common issues that new rigid heddle weavers will encounter:
- Uneven edges (selvedges):
- Causes: inconsistent tension, improper beating, fraying edge threads, inappropriate warp threads used.
- Solutions: Ensure proper warp tension to begin with, try to beat evenly, be sure to use a yarn that is suitable for warping. If edge threads are too loose, try using weights on those threads over the back of the loom. If they are too tight and middle threads are looser, try some wedging techniques as demonstrated in this video.
- Broken warp threads:
- Causes: tension too tight or uneven (so some threads end up super tight while others are loose), friction from the heddle (some yarns are more susceptible to this than others).
- Warp yarn is not strong enough to be suitable for warping.
- Solutions: choose a suitable warping yarn, ensure warp tension is not exceedingly tight, angle your weft before beating so it has room to settle rather than drawing in too much at the edges.
- Skipped threads:
- Causes: threading errors, uneven tension, incorrect angling of a stick shuttle as it travels through the thread. These problems will create floats and imperfections in your work.
- Solutions: check threading, rethread problem areas if needed. Be vigilant with how you use your shuttle so it’s not inadvertently picking up warp threads it shouldn’t.
- Gaps, uneven and slightly scrapping weaving:
- Causes: uneven beat, inappropriate sett, slippery yarns.
- Solutions: Getting a feel for a correct beat takes time and practice. For a balanced weave, you want a balanced beat. Try to think of pressing your weft into place, we are not whacking here! Hop up and view your work from a few different angles every now and then. Take photos of your progress and review. (Why? For some reason, mistakes stick out like a sore thumb when viewed as a photo! 🤷♀️) Again, an uneven warp will impact how your weaving appears. An incorrect sett will have a big effect on your finished weaving, so make sure you figure out the ideal sett before commencing.
It’s good to remember that challenges are part of the weaving journey. I have never personally made a weaving mistake that I couldn’t fix, which is very encouraging!
Having a community to turn to when your weaving is not going so well is invaluable. If you can’t meet with other weavers in person, online groups like my free Facebook group are wonderful for networking and inspiration.
Perhaps you’re ready to level up your weaving in a really supportive atmosphere with a library of online classes at your fingertips? Check out the Online Weaving School!
I hope these tips have been helpful to you, feel free to share your favourites in the comments below.
I have also put together a downloadable Rigid Heddle Loom Setup Checklist as a free resource just for you, enjoy!
Until next time…
Happy Weaving!