One of the major challenges when you’re new to weaving is knowing exactly what tools you need. If you’re particularly budget conscious (and most of us need to be!) you don’t want to spend money only to find that you didn’t actually need or use the new tool.
Today’s Ask Kelly question is one about two heddles and whether it is worth the investment to purchase an additional heddle in the same size as an existing heddle. At first glance you might think, well I already have one 10 dent heddle, why on earth would I buy a second 10 dent heddle – isn’t that a complete waste of money?
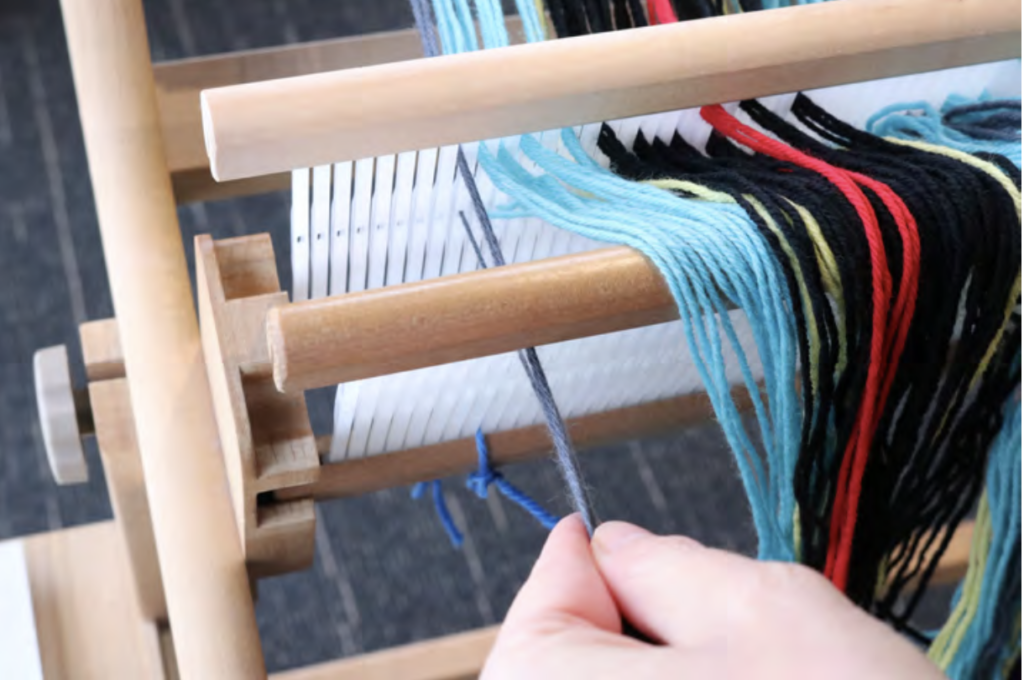
Let’s delve into this discussion so you can find out why two heddles might be a worthwhile investment for you (or not!)
“Could you please suggest where I would get some information on why I would want to weave with two heddles on the flip. I am not new to rigid heddles but far from advanced. Some people have suggested two heddles is a waste and I should just leap to a 4 shaft. I want to make an informed decision about whether to invest in additional heddles for the flip. I appreciate your guidance. I have not yet done your classes on doing two heddles. Thanks so much.”
Marla
Hi Marla,
That is a very loaded question with a lot to unpack, but I’ll try to keep it brief and to the point.
I guess one of the main reasons a rigid heddle weaver would buy additional heddles is to increase shaft capability without having to invest in another loom.
Yes, new heddles are costly, but if you compare that cost to a brand new 4 shaft table or floor loom it is a small investment.
I wouldn’t ever say that additional heddles for a RH loom are a waste, they are just another way to achieve a desired outcome.
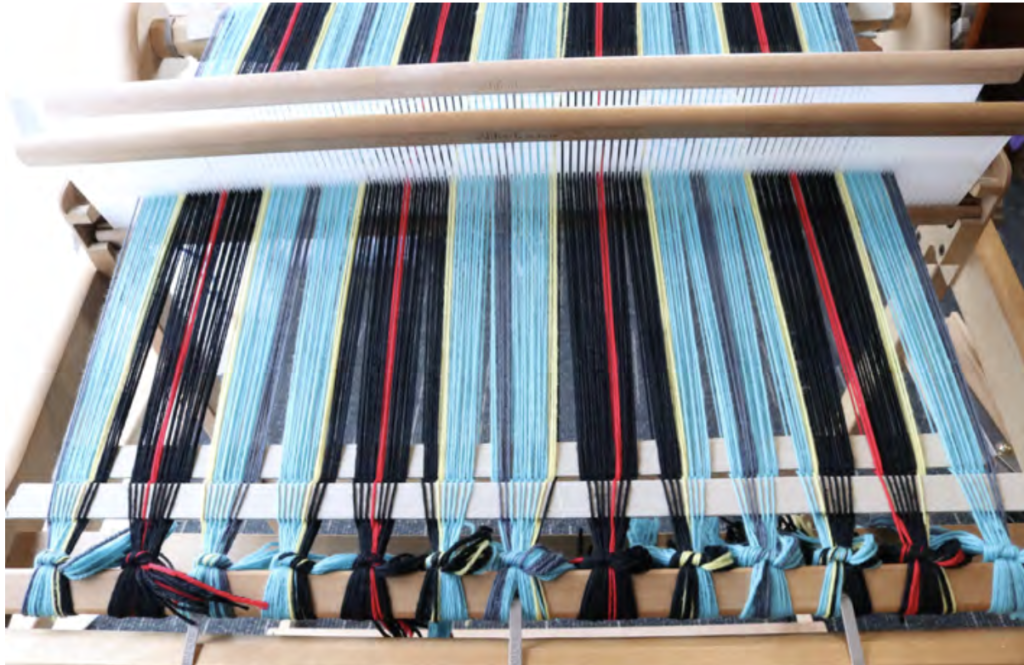
As demonstrated in my Weaving With Two Heddles online class, there are a lot of possibilities by adding just one extra heddle. You can weave a variety of 3 and 4 shaft (with the addition of heddle rods/pick up sticks) patterns, you can double your sett or you can weave double width or tubular.
Some of the questions I would be asking you are: Do you want a new loom? Are you interested in weaving on more shafts? Would it help you to have more than one loom so you can more projects going at once? Do you have the space for another loom? The budget?
The Schacht Flip rigid heddle loom differs a little to the Ashford rigid heddle looms in that the heddle positioning is not the same when using more than one heddle and some weavers are confused by that. But, as with everything in weaving, there are workarounds and you can find some more information about that on the Schacht website here.
You might also find these articles of interest:
Doubling sett in rigid heddle weaving…
I hope this article has been helpful to you, feel free to share it with others so more can benefit. Leave your comments or questions underneath this article and
Until next time…
Happy Weaving!
*This post contains affiliate links. For more information, please see my disclosure policy.