The Heart Scarf is my free project for the year of 2021. Let me give you a little bit of background as to why I’m doing this and how I came about designing this project.
Last year, when the pandemic hit, I released the Wash Your Hands Towels project, which was a hugely popular project. I know that all of you appreciated so much, having something concrete, beautiful and creative to be able to fix your minds on in a time where there was such uncertainty.
I loved doing that project so much for you that I wanted to do something similar this year. And something that has really been on my heart and in my mind for most of this year in particular, is that I know there are so many people out there that as a result of everything that’s been happening in the world are chronically lonely.
*This post contains affiliate links. For further information, please see my disclosure policy.
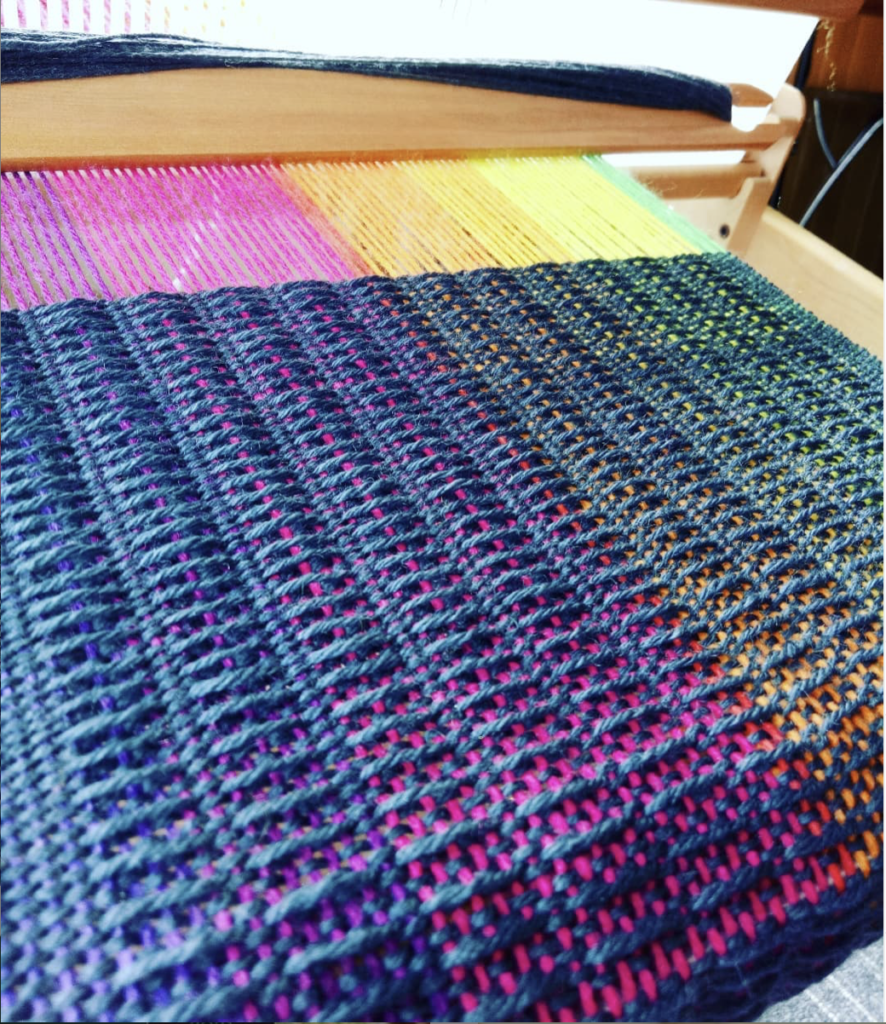
So I wanted to create a project whereby you as the weaver would be weaving this beautiful scarf called The Heart Scarf. And you’d be weaving it with someone in particular in mind, someone who may be struggling with loneliness, perhaps they’re not able to get out and see their family and friends like they normally would.
Or you might know someone who’s struggling, feeling down, perhaps they live alone, or they have some other difficulties that cause them to feel that loneliness, really, that’s one of the most heartbreaking things for me to think of is that there are people out there who are just desperately lonely.
If we, as the makers of beautiful things, can do anything to make someone’s day a little bit brighter, then that’s definitely something that I want to be a part of. And I know that many of you would want to as well.
I’ve written a short poem from my heart. This poem is available to print out in either cursive or print, along with the free pattern. Once you’ve finished your scarf, you can package it up with the poem if you so choose, or perhaps with something that you want to write yourself and send it off to the recipient.
Perhaps you’re feeling really lonely yourself, perhaps it’s been an awful year for you, perhaps you’re having a hard time for other reasons. If that’s the case, I would love for you to weave this scarf for yourself and you can consider the words of the poem from me to you.
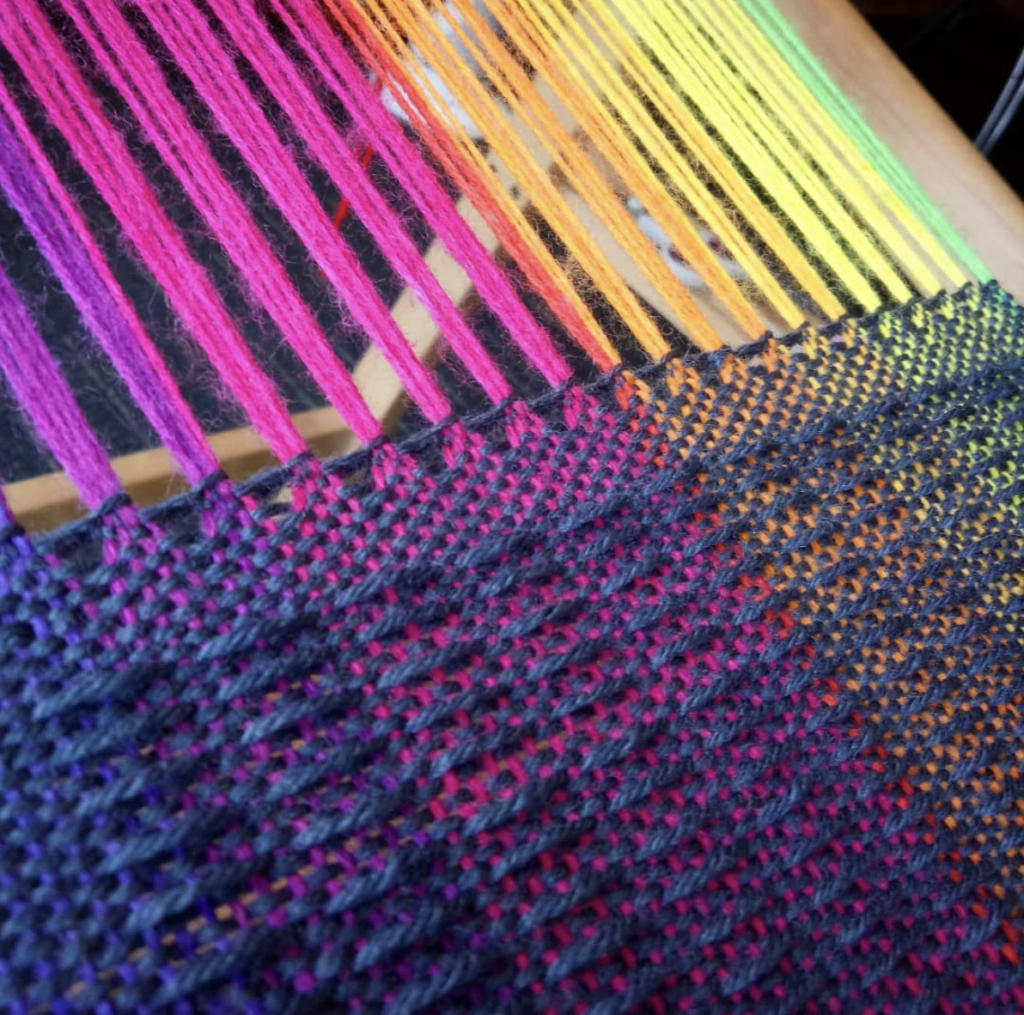
Let’s get down to the nitty gritty and go over the project details, starting with what you need to complete this project:
A rigid heddle loom.
Now, the width of my scarf on the loom is 11″ and I used my 24″ rigid heddle loom. BUT, if you have a smaller loom, you can absolutely weave this scarf. If you have a 10″ Sampleit or a Cricket, just warp the full width of the loom for a slightly narrower, but equally lovely scarf.
A 7.5 dent heddle/reed.
Again, this doesn’t have to be sett in stone. (Get it? Sett in stone?) If you don’t have a 7.5 dent heddle, you can use your 8 dent. If you want to change the heddle size completely, yes, you can – but you would also need to change to a more appropriate yarn size, so just bear that in mind.
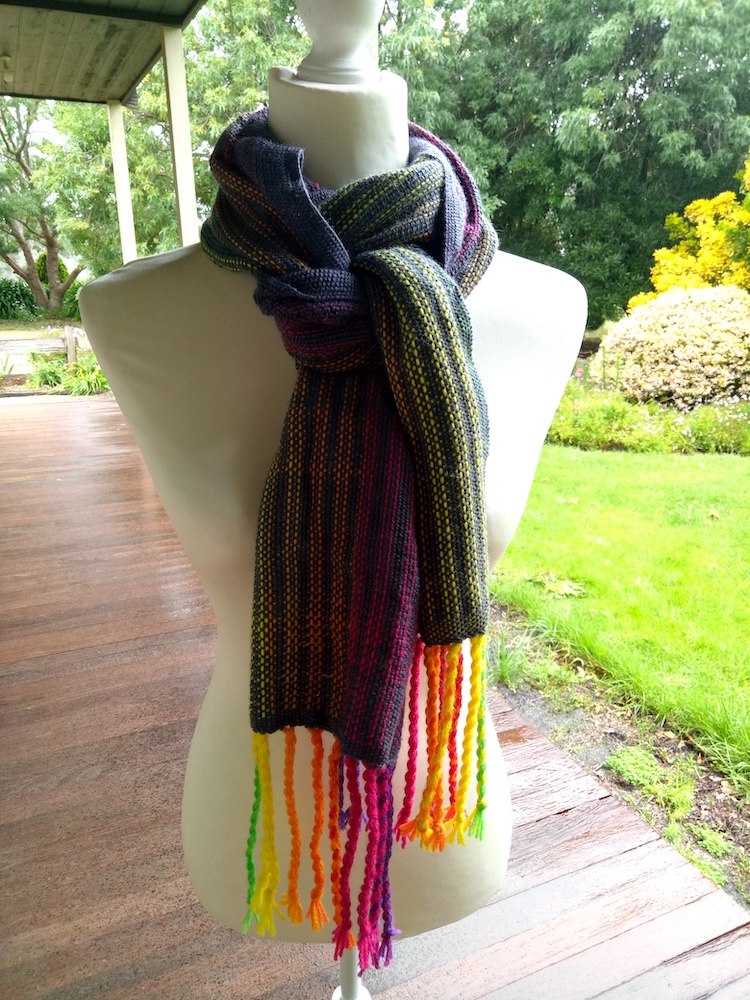
Pick up stick
We use a single pick up stick to create the beautiful, textural scarf pattern. The pattern is simple to pick up with your stick and also simple to weave with a 4 step repeating weaving sequence.
Stick shuttle
You only need one stick shuttle for this project, as we use the same weft yarn and colour throughout the project. As long as it’s wider than the width of the piece on the loom (11″), you’re good to go.
Tapestry needle
This is an essential for hemstitching. My favourite tapestry needle of all time is the Clover Gold Bent Tip Needle. I’ve talked about these needles before, but I love them for several reasons:
- They slide through hand woven fabric beautifully
- The bent tip makes it really easy to dive down and come up through the fabric without having to perform hand contortions!
- They are affordable
- They are gold! Who wouldn’t love that?! (And if you’re prone to, ahem… losing things, the gleam of the gold is quite helpful!)
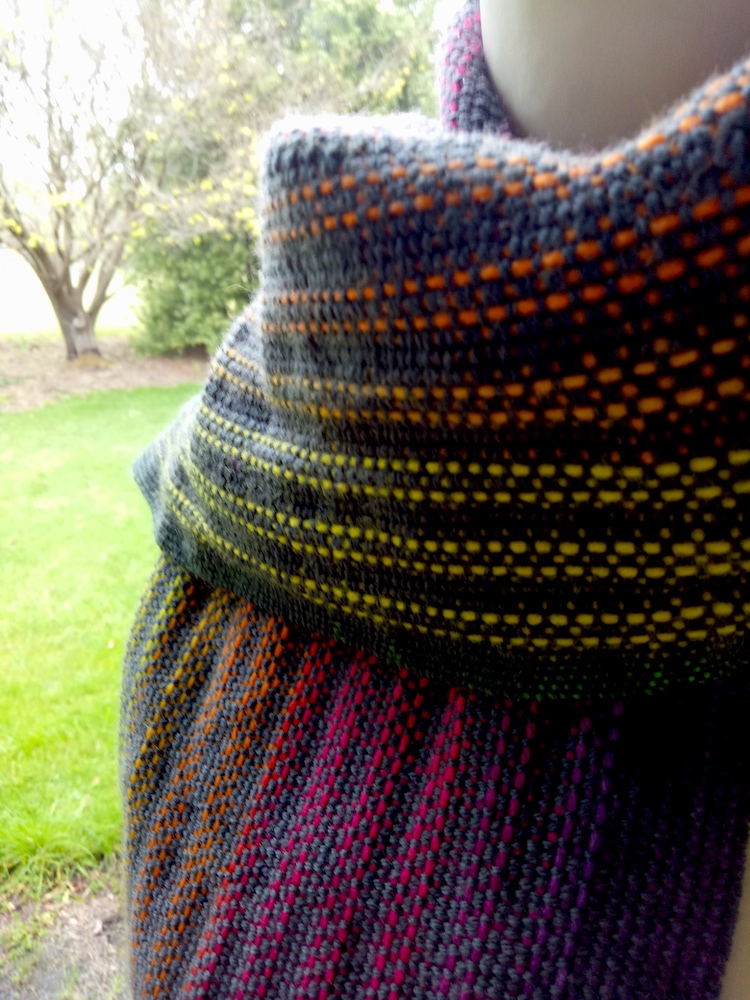
Fringe Twister
Whether you twist your fringe or not is optional, but it is a beautiful way to finish your scarf. I talk about some other options for fringes in the finishing video if you want to choose a different way. There are many brands of fringe twisters available, I have had a LeCLerc Fringe Twister for many years and have been very happy with it.
Reed and threading hook
Most rigid heddle looms will come with one or both of these, but I would like to recommend the Ashford Doubled Ended Hook for it’s durability, ease of use and affordability. I have a whole bunch of these little hooks around my studio and my old metal threading hook that used to split all my threads doesn’t get a look in anymore.
Yarn
To see all the yarn details, please download the pattern. For the warp, I used Lion Brand Mandala yarn in Gnome, dk weight. This yarn is an acrylic, but I have some other suggestions in the pattern if you prefer to look at other options. My weft yarn was a super wash wool in dark grey in a fingering weight.
Weaving level
I designed this project to be achievable for beginners but interesting enough for more experienced weavers. If you are an absolute beginner, I recommend that you take my Woe to GO! Beginner’s class before attempting a project like this.
How to get the pattern
The file underneath has a “download” button at the bottom. Click on that to download, then choose either to print the file or view it on your screen. The pattern PDF includes all the details you need for the project, including yarn amounts, materials, pick and weaving sequences plus the poem in either cursive or print – your choice!
You can view the first of 6 videos on Youtube –
The full video lessons and printable pattern are also available all in one spot at the Online Weaving School if you would prefer to watch there.
I hope you love this project and bring joy to someone’s life (or to your own!) by taking part.
Until next time…
Happy Weaving!