Many years ago, there was a beautiful little yarn and embroidery shop in an upmarket seaside suburb around 30 minutes drive from my home. Visiting was a treat, as the shop was in an historic stone building, had several rooms and was wonderful just to look at.
I couldn’t afford to spend much on yarn or supplies back then, but I once splurged on some beautiful cashmere yarn to knit a hat for my newborn, and I even once went to the extravagance of buying a pretty floral handkerchief for each of my girls, just because I wanted them to have something pretty.
*This post contains affiliate links. For further information, please see my disclosure policy.
One time, my husband drove past this shop with a new work colleague. She pointed at the shop and said “that’s for people with too much time on their hands”.
My husband was slightly bemused, knowing that I was a customer of the shop. He also knew that, at that moment, I was at home, caring for and homeschooling our 4 young children. On a good day, I was able to take 30 minutes to 1 hour to work on a craft project. Many days, I was either too busy or too exhausted to even consider doing something creative. I certainly didn’t fit the profile of someone with too much time on her hands!
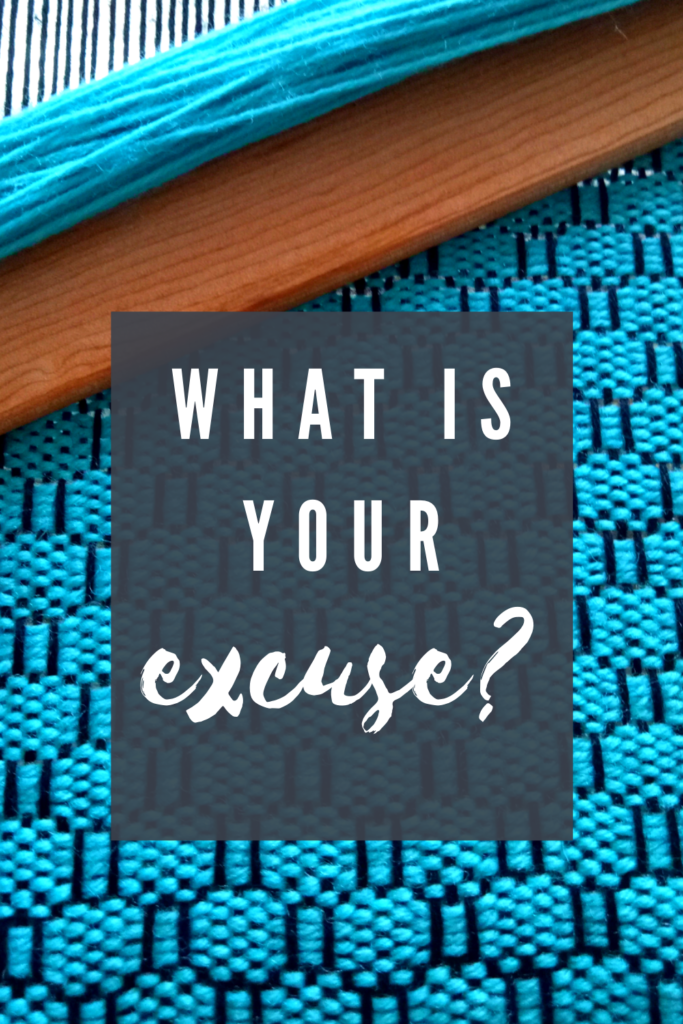
Time is a funny thing. Our ideas and beliefs about time are funny too. Often when people say they “don’t have time” to do something, it is really just a bit of a cover up. An excuse.
An excuse to not have to exert effort in order to learn something new. Maybe they know they have to save some money to buy the necessary materials to start learning and that is something they don’t want to do. Maybe (and I think perhaps this is the most common reason people make excuses) is to hide the fact that they are afraid of failing.
Since I started my Online Weaving School almost 4 years ago, I’ve heard from thousands of weavers all over the world from all walks of life. Many are brand new to weaving, some have been weaving for some time, and others have not yet begun but have a desire to start.
I’ve heard frequently from people who say they have been wanting to learn to weave for 20, 30, 50 years! Overwhelmingly, new weavers have told me that they wish they had started earlier instead of waiting for “the right time”.
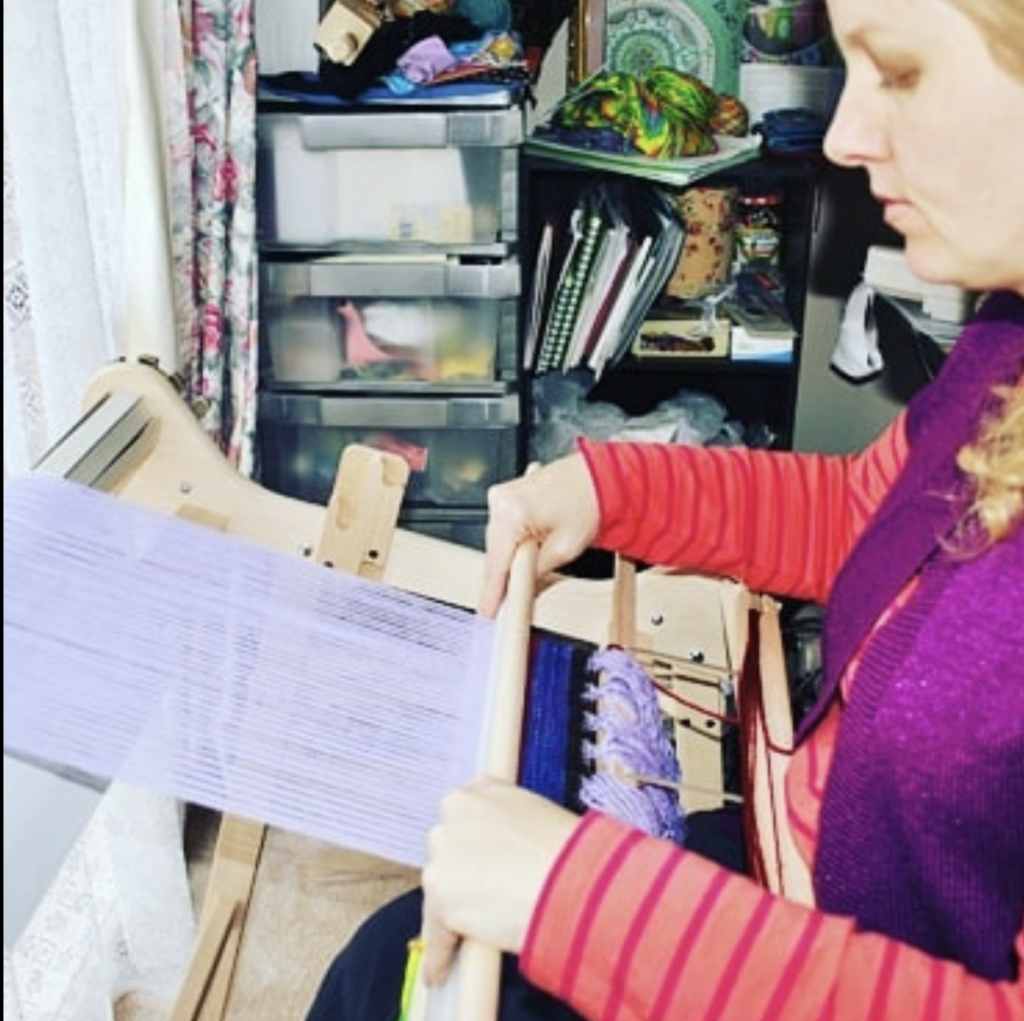
You see, the majority of people live their lives in a box of societal expectation.
Finish school. Go to college. Get married. Have a family. Somewhere in amongst all of that, buy a house. A couple of cars. Work. Raise your family. Keep working. Kids are grown up and left home? Now you have more time to work! Accumulate more stuff with the money you earn from working. Indulge in expensive holidays in an attempt to recuperate from working. Go back to work, after all, someone has to pay for the lifestyle I’ve just described. And then…. one day, finally, you get to retire! THEN you have the time to do all the things you have been really wanting to all these years. You’re likely in your early 70’s by this stage.
None of the above are bad things, they are good things. It is good to get married and raise a family (in fact, I think it’s one of the best things anyone can do!) It is good and necessary to work. Holidays are lovely. Having things you want is nice. But these things are not exclusive, and they don’t have to be compartmentalised.
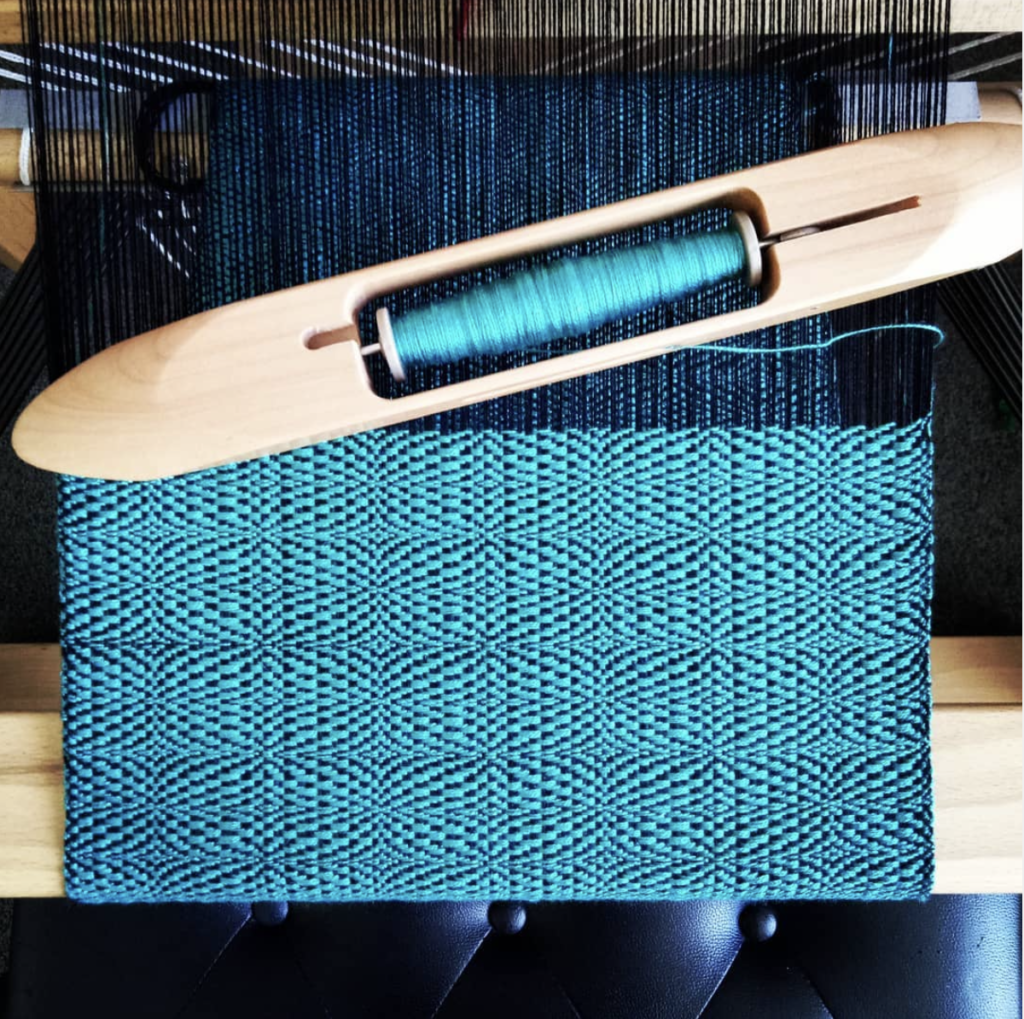
I have not approached my life as a checklist of things to be done before I can invest in myself and my passions. I am raising children right now, still homeschooling, caregiving and providing. My role as a wife and mother are very important to me. And yet, it is also very important that I get time to be creative and work on things I love. Doing so makes me a better wife, mother and person. It’s part of who I am.
When I began weaving, we had small children and very little money. Yes, I too had my mental excuses as to why I couldn’t learn to weave. Not enough time. No spare money. I needed to wait for the right time. I might not be smart enough to do it.
But, with my husband’s help, I became convinced that it was a good thing to do, and we worked past the excuses to make it happen. To say that the decision to save for and purchase my first rigid heddle loom has been life changing would be putting it very mildly!
And it’s not just me, only yesterday a student told me that learning to weave has been “life affirming” for her.
If you have been wanting to learn to weave, but for “some reason” have not started, I encourage you to look at your situation realistically. Are your reasons actually excuses? Are they a cover up for something else?
I want to talk just a little more about time. We all have the same 24 hours in a day. We also have choices about how those hours are used. Do you work all day, get home and collapse in front of the tv? This might seem a little harsh to some, but I am sure that if you have time to watch tv, you have a lot more free time than you might think. Do you spend hours surfing the internet or on social media? Then, guess what? You have time to learn something new!
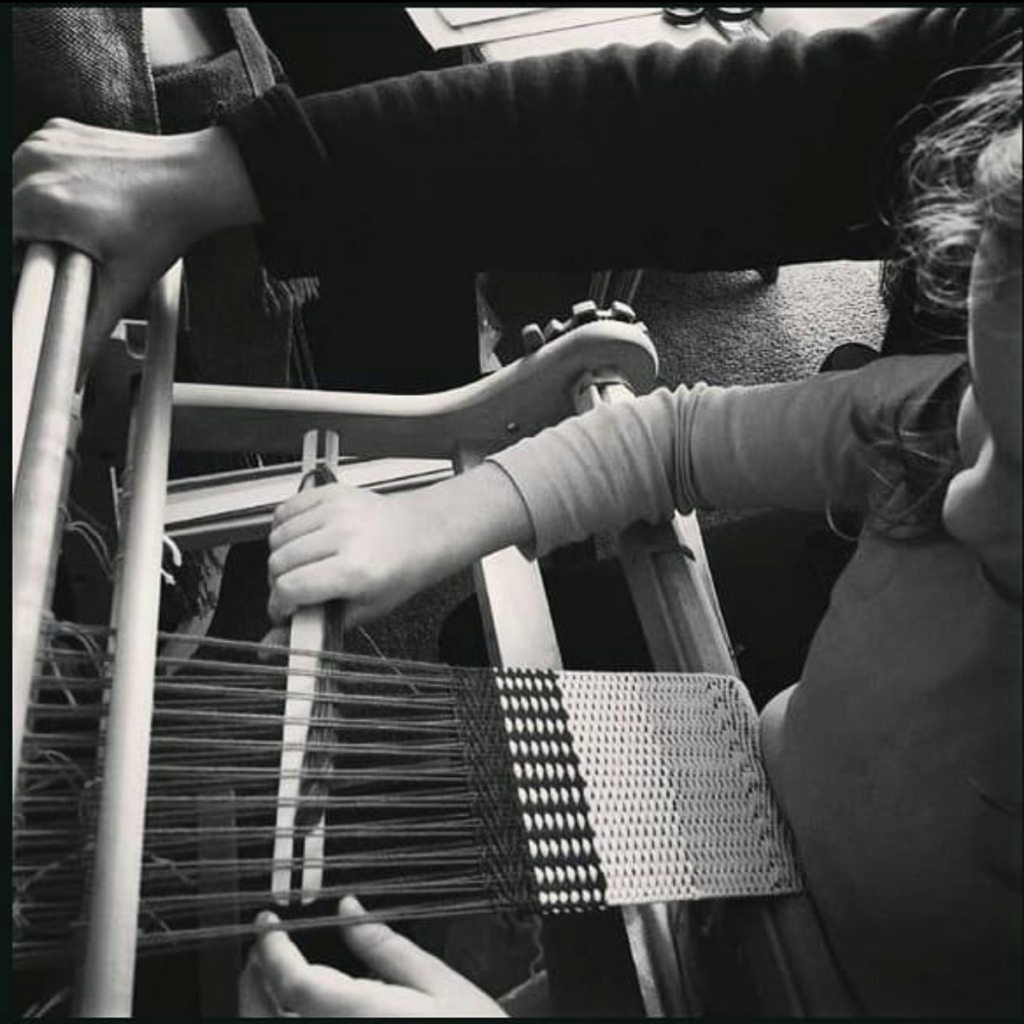
Overrun with little kids? Yep, I’ve been there and I would use their nap or sleep times in order to do something creative. If that didn’t work out, I would involve them in what I was doing in order to get that time for myself. Sometimes that would be having a child sort through my button or ribbon collection, which they thought was awesome fun. Sometimes it would be having a child sit on my lap while weaving to “help” me beat.
Last year, I wrote a post about planning and prioritising in your days so that you could make time to do the things you really wanted to. I included a printable daily planner that I hope some of you might use to make some plans and goals.
What I want you to get out of this post at the very least is that you don’t know what you don’t know. You need to take that first step of trying and then another step, and then another. The point is to make a start, because retirement could be a long time away!
……………………………………………….
One more story that struck me when I read it in a magazine and has stayed with me for years. An older woman was sitting in a doctor’s waiting room. She was knitting while she waited.
A man who was also waiting and had been observing her, suddenly asked “Why do you waste your time doing that?”
The woman replied “When I leave here, I will have half a dish rag, what will you have?”
……………………………………………………
What I want you to get out of this at the very most is that you are worth it. You’re worth the time, money and effort investment and I know that if you truly want to, you can do it!
If you would like to view this post in video format (and watch me weave), I invite you to watch here-
Until next time…
Happy Weaving!