When you have a desire to start selling your handmade items, it can feel like an overwhelming leap to take.
But it doesn’t have to be. There is no rule that says to start selling you need to launch a full on business with all the bells and whistles. That is certainly not the way I started out.
- This post may contain affiliate links, please see my disclosure policy for further information.
If your budget is tight or you are wanting to just dip your toe in the selling game to find out if it’s something you want to continue to do, I have 3 ways that you can start selling online for free!
Now, just as a little disclaimer, a couple of these methods are not necessarily 100% free, due to payment processing fees. But, as far as actually making an item available for sale, these methods do not cost you anything until you’ve actually made a sale (and even then, I’m going to talk about other ways to take payments without fees).
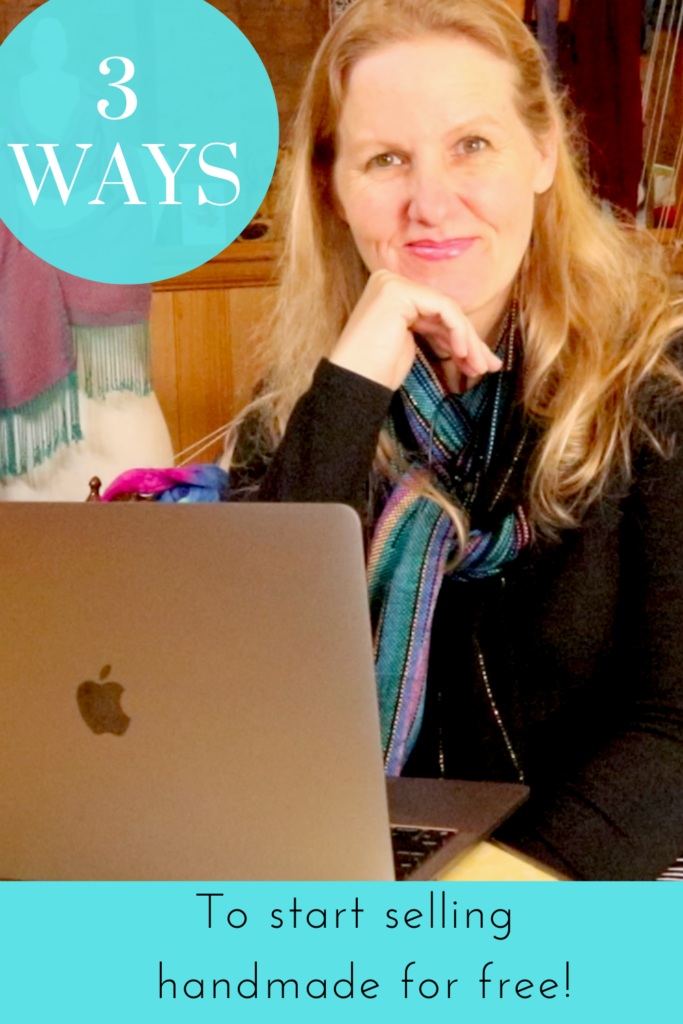
Firstly I’m going to talk about the pros, or positives of these methods. I’ll cover the cons (negatives) at the end.
Now that we have that out of the way, here are my 3 recommendations for starting out selling for free online:
- Social Media
2. Mailing List
3. Family and friends
Let’s look at each one in more detail.
SOCIAL MEDIA can include Facebook, Instagram, Twitter, TikTok and others. Today I’m going to be talking about Facebook and Instagram, as these are the platforms where I have specific experience selling handmade.
A misconception is that you need to have a large social media audience in order to sell anything. Let me tell you, the quality of your audience is way more important than the quantity.
A small audience of people who are genuinely interested in what you do is so much more valuable than a huge pool of people who couldn’t really care less.
On Facebook, groups have been a good way to sell in the past and could still be relevant, depending on the group. Make sure the group is very relevant to what you sell and educate yourself as to the rules. You don’t want to get booted out of groups for infringing on the rules!
Another way to sell on Facebook is to simply make posts. I will be going into more detail with this when I talk about Instagram, but basically you can make a selling post either on your personal Facebook profile or you can make a business/fan page.
I recommend the business page route, as your Facebook friends may not appreciate feeling like they are being spammed with sales posts. A business page is a more appropriate place for these styles of posts.
Now we will look at Instagram. I have recently been testing selling on Instagram, (not following me yet? You can find my account here.) with successful results. I’m going to show you my exact post from last week that I used to successfully sell a weaving kit.
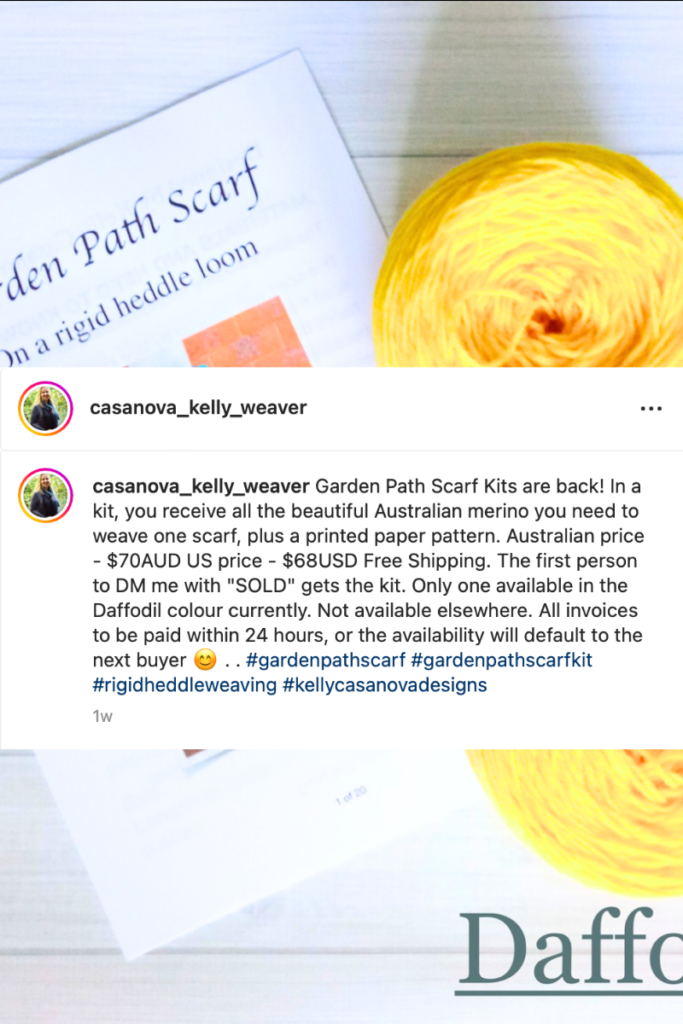
Again, check the rules of any platform you’re using first to ensure no violation of rules is occurring.
If you look at my wording for this sales post, you will notice that it’s very clear and provides all the detail the buyer needs to make a well informed purchase, without being too wordy or overdone.
Importantly, I’ve clearly stated my terms for payment, the exact items that the buyer will receive, the price, and a good quality photo of the item. The invitation to be the first buyer to DM (direct message) me with “SOLD” creates a sense of urgency and competition.
This particular kit sold within 8 seconds of posting and the invoice was sent a paid for well within the 24 hour time frame.
I use PayPal to create and send invoices, but this is where this method is not completely free. There are payment processing fees through PayPal – usually a few dollars but it does depend on the value of the item sold. I factor these fees into the total cost of the item before I sell it. The “free shipping” is also calculated beforehand so that I’m not paying for that out of my own pocket.
Going through PayPal means that once the sale is made, I get the buyer’s email, make up their invoice (which takes less than 30 seconds) and send. As soon as the buyer has paid the invoice, PayPal emails me with the buyer’s shipping details and notification of payment.
You could still get around these fees by doing something like a direct bank transfer, but that is not such a popular way to make online payments these days. I recommend researching and experimenting to find a happy medium that suits you.
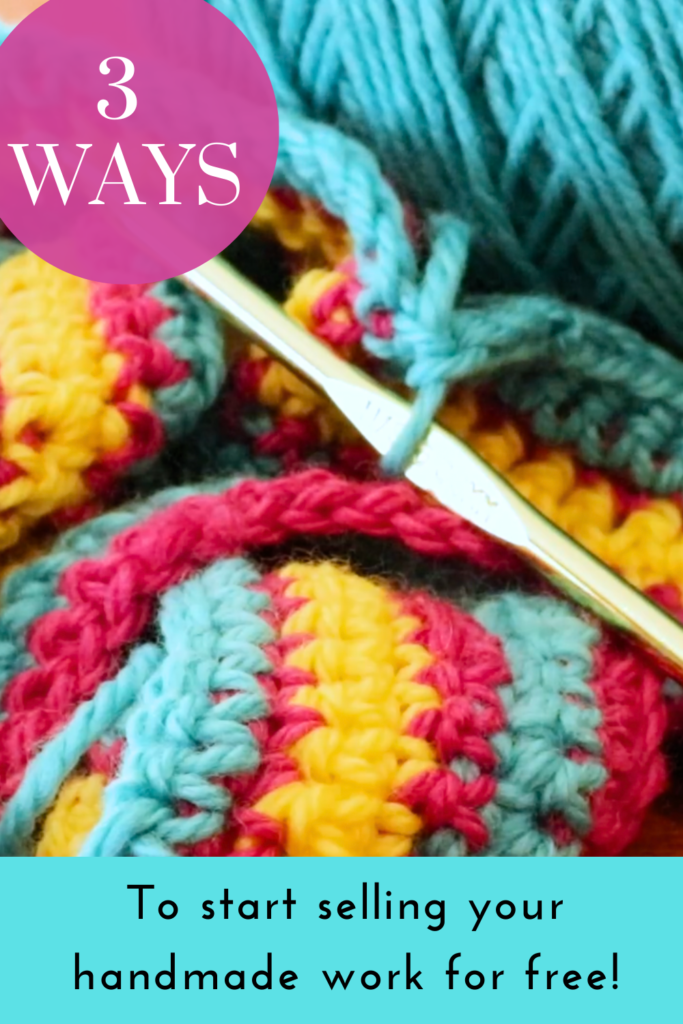
Now we will talk about selling through EMAIL. If you have watched any of my business videos or read any of my posts, you will have already heard me talk about how essential it is to have a mailing list to build an audience.
Want to start selling your handmade items but don’t have a mailing list yet? Start one today! You can get started with Convertkit (my email provider) for free.
Contrary to popular belief, you do not need a huge amount of subscribers on your email list in order to make money. The quality of subscriber is so much more important than the quantity. A quality subscriber is already interested in your work (that’s why they joined your list!) and they may be interested in purchasing from you.
Selling through email is very similar to making a social media post. The key is to not make every email a sales post, that can make your audience feel like they are constantly being inundated and they may unsubscribe.
What I like to do is to provide my mailing list with valuable and good quality news and information and include a small section on the item I’m selling. Very recently I sold another Garden Path Scarf kit this way, by sending out my weekly email, The Weekend Edition.
In this weekly newsletter, I provide links to blog articles and videos, update my audience on what I’ve been working on and basically share whatever I feel will be interesting to them. For the kit, I did the same as I would for a social media post – the clear photo, all the details, my terms and conditions. Again, this kit sold rapidly and I had multiple buyers who missed out.
If you want to take a look at how it might look to have a mailing list, I recommend that you sign up to mine for inspiration.
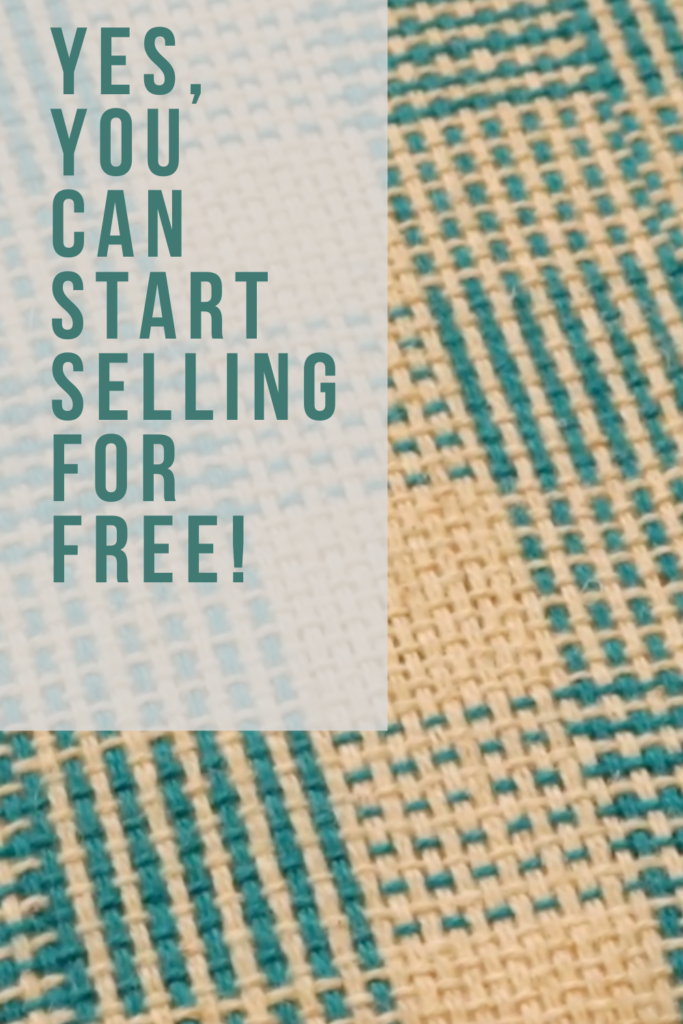
The third and final way that you can start selling online for free is through FAMILY AND FRIENDS.
This is such an easy and organic way to get started, without the pressure of selling to people you don’t know. It can be so natural that you don’t even realise a sale is happening until it’s done!
It could be as simple as someone in a social situation asking you what you do, or what you’ve been doing and you tell them about your craft. They may ask more questions and become interested. This can lead to them asking either whether you have a specific item for sale that they want or whether you would be interested in making them something (custom order).
To sell in a relaxed situation, perhaps in your home or someone else’s requires no technical knowledge of online processes or payments – often you will be paid in cash in this type of scenario. You don’t need to take photos or make online posts.
Friends and family will also likely advertise for free on your behalf, by telling others about what you do and what you sell. Perfect!
OK, I’ve talked about how great these three methods are, but are there any downsides?
Yes, but they are very minimal, I think the positives outweigh the negatives here.
- If posting to sell online, make sure you’re aware of regulations to ensure you don’t violate rules and possibly lose your account.
- These methods are not automated. If you’re selling on Etsy for example, the work is all done beforehand, the listing is published and then Etsy takes care of the rest once there is a sale (apart from you sending out the physical product). If using any of these 3 methods, all the steps of the process are up to you (including sometimes having to chase buyers for payment and sometimes hearing crickets in return š).
- If you’re selling a larger number of items, you will definitely want to be able to automate your process more. These free methods are better for the seller just dipping a toe in, or selling items occasionally rather than frequently and at a higher volume.
I have some additional resources for you if this is a really interesting topic for you:
Do You Want To Start Selling Your Weaving?…
Selling for Weavers Online Class (members only)…
Starting a Weaving Business in 2023…
10 Things I’ve Learned about Etsy in 10 Years…
I hope these ideas have been super helpful to you. If you want to see this post in video format, you can view that here:
Until next time…
Happy Weaving!