One of the marvellous things about owning a rigid heddle loom is the ability to try out so many weave structures without having to upgrade looms if you don’t want to.
It’s a great way to try out a structure to test whether you enjoy it and want to pursue it further. This can help you to make future weaving and loom decisions.
One structure you may be interested in trying out is tapestry and that is what today’s Ask Kelly question all about. I apologise to the original author of the question, I have misplaced your name!
“I have a question about rigid heddle looms used for tapestry.
It is my understanding that the downside of using the rigid heddle is the fact that the use of the heddle causes the warp threads on the outside to be too loose and the threads in general are also too loose for tapestry weaving. If you wanted to use the loom without the heddle, would that be possible? And / or ok to work better.”
When I got started with tapestry weaving, it was on a rigid heddle loom. It was a great experience, as I was able to learn the basic tapestry techniques and it also taught me that tapestry was something I wanted to pursue, so I eventually bought a dedicated tapestry loom.
Regarding the possibility of looser outside threads, there is a trick you can use to ensure that your edge warp threads on your RH loom are under the same tension, I have a video on that here-
I guess the answer to your question about warping without a heddle is yes, you can. I haven’t done that myself, and I would use the heddle initially to warp, in order to space the warp to the sett I wanted.
Having said that, it is very handy to be able to change sheds quickly with a heddle.
I do have a tapestry class for rigid heddle weavers, if you’re interested in checking that out-
Tapestry Weaving on a rigid heddle loom…
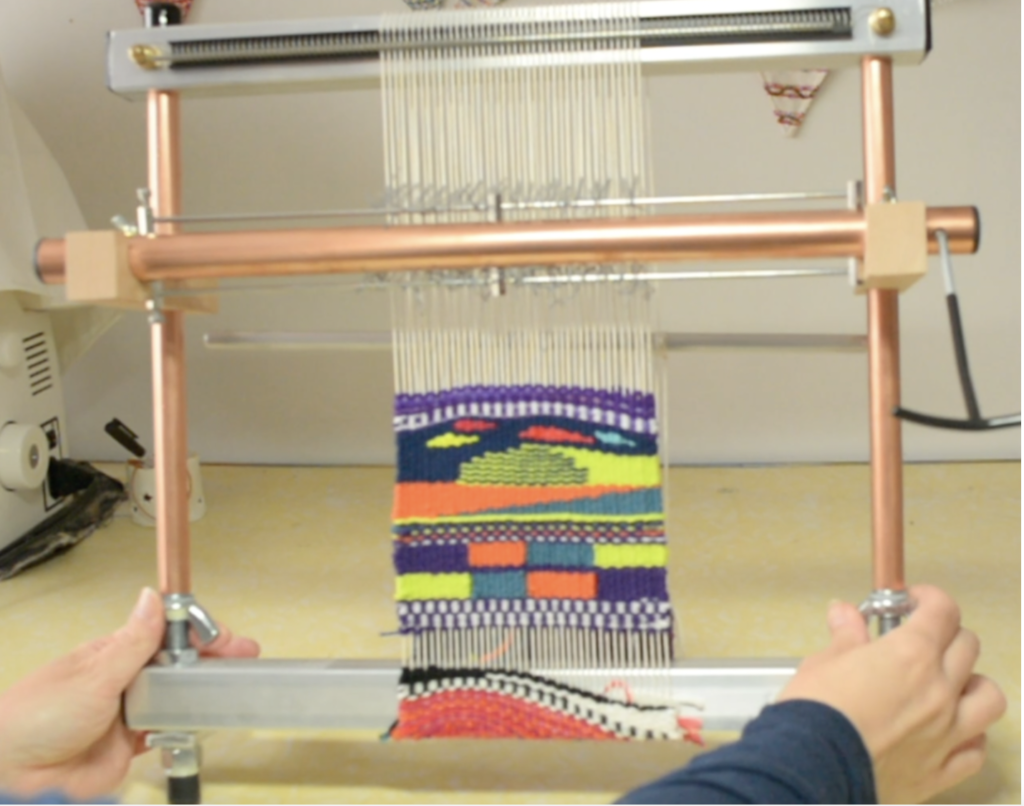
I chose the Big Sister Tapestry loom from Mirrix because of their reputation for quality, the sizing options and the ease of set up and use. I have a review of the Big Sister Loom here and an interview with the CEO and founder of Mirrix Looms here.
So, you may wonder what the main reasons would be for a rigid heddle weaver to upgrade to a tapestry loom?
- A dedicated tapestry loom means you are not taking up precious loom space. Tapestry is a slow process, and you may want to use your rigid heddle loom for other projects rather than wait until the tapestry is finished.
- A tapestry loom has far superior tension to a rigid heddle, which gives a better result for tapestry weaving.
- Most tapestry looms are upright, which is more suitable for working tapestry.
- Tapestry looms are strong and suitable for holding high tension, whereas a rigid heddle loom is not designed for super tensioning.
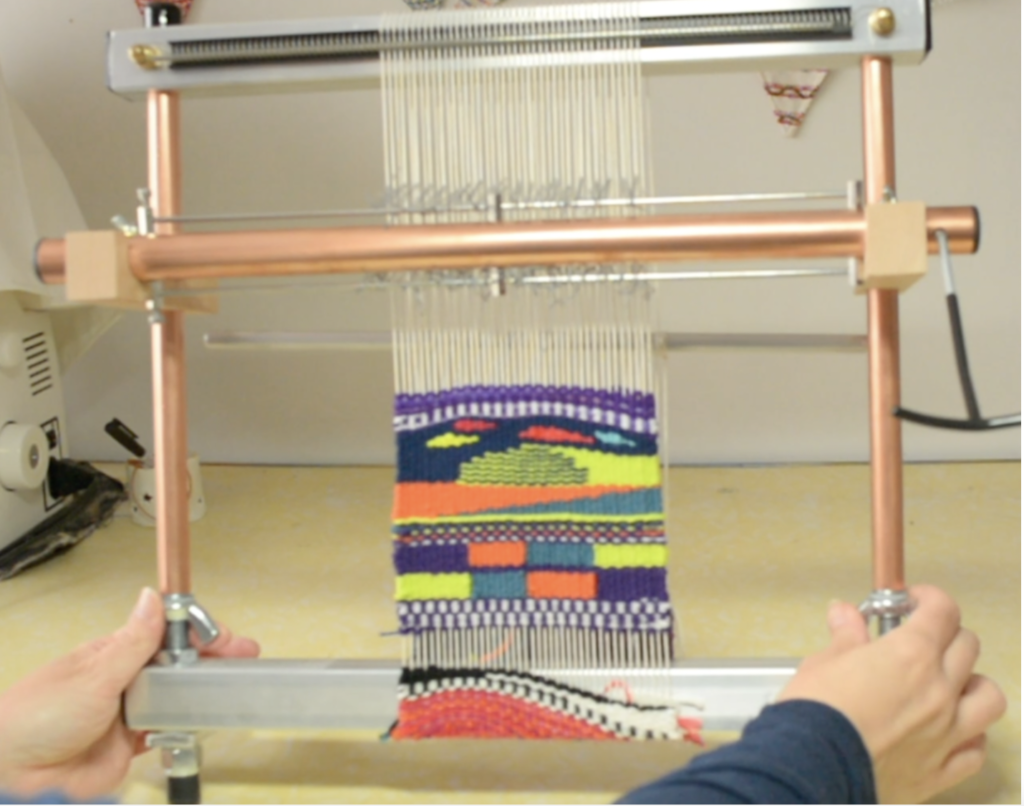
I hope you enjoyed this article and until next time…
Happy Weaving!
This post contains affiliate links. For further information, please see my disclosure policy.